Excitement About Alcast Company
Table of ContentsUnknown Facts About Alcast CompanyThe 6-Minute Rule for Alcast CompanyThe Ultimate Guide To Alcast CompanyMore About Alcast Company10 Simple Techniques For Alcast Company7 Simple Techniques For Alcast Company
Chemical Contrast of Cast Aluminum Alloys Silicon promotes castability by reducing the alloy's melting temperature level and improving fluidness during spreading. Additionally, silicon adds to the alloy's stamina and wear resistance, making it useful in applications where sturdiness is crucial, such as vehicle parts and engine elements.It likewise boosts the machinability of the alloy, making it simpler to process into completed products. In this means, iron adds to the general workability of aluminum alloys.
Manganese adds to the toughness of light weight aluminum alloys and enhances workability. Magnesium is a lightweight component that offers toughness and effect resistance to light weight aluminum alloys.
How Alcast Company can Save You Time, Stress, and Money.
Zinc improves the castability of aluminum alloys and assists manage the solidification process throughout casting. It enhances the alloy's stamina and firmness.

The primary thermal conductivity, tensile stamina, yield strength, and elongation differ. Select appropriate raw products according to the efficiency of the target item created. Amongst the above alloys, A356 has the highest possible thermal conductivity, and A380 and ADC12 have the most affordable. The tensile limitation is the contrary. A360 has the very best return strength and the highest elongation rate.
Alcast Company Can Be Fun For Anyone
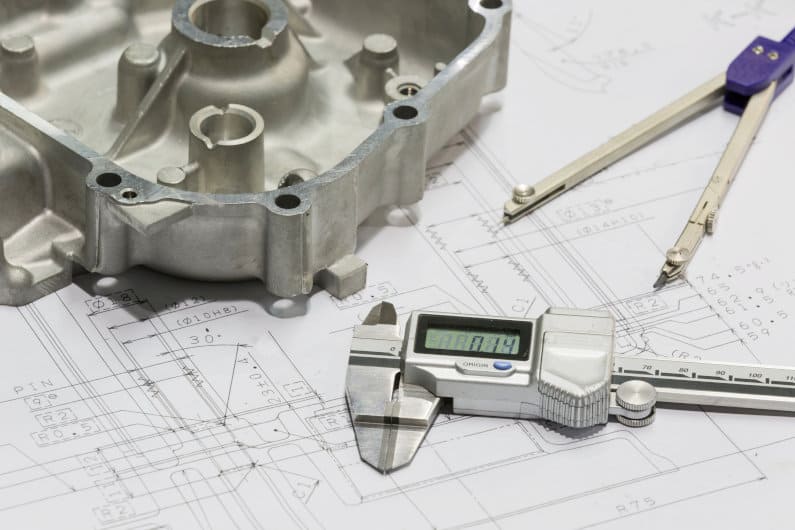
In accuracy spreading, 6063 is well-suited for applications where complex geometries and top notch surface coatings are critical. Instances include telecommunication enclosures, where the alloy's remarkable formability enables for sleek and aesthetically pleasing designs while keeping architectural honesty. In the Lighting Solutions market, precision-cast 6063 parts develop sophisticated and reliable lighting fixtures that need elaborate shapes and great thermal efficiency.
It causes a better surface finish and far better deterioration resistance in A360. Furthermore, the A360 displays superior elongation, making it perfect for facility and thin-walled elements. In accuracy casting applications, A360 is fit for sectors such as Customer Electronics, Telecommunication, and Power Tools. Its enhanced fluidity permits complex, high-precision parts like smart device housings and communication gadget housings.
The 9-Minute Rule for Alcast Company
Its unique residential or find out here now commercial properties make A360 a valuable option for precision casting in these markets, enhancing product resilience and top quality. aluminum casting company. Aluminum alloy 380, or A380, is a commonly utilized casting alloy with numerous distinctive qualities.
In accuracy spreading, aluminum 413 shines in the Customer Electronic Devices and Power Tools industries. This alloy's remarkable corrosion resistance makes it an exceptional selection for outside applications, ensuring resilient, long lasting products in the pointed out sectors.
See This Report on Alcast Company
When you have determined that the light weight aluminum pass away casting procedure appropriates for your task, an important next action is picking one of the most suitable alloy. The aluminum alloy you pick will significantly impact both the casting procedure and the residential or commercial properties of the final product. Since of this, you need to make your choice very carefully and take an enlightened method.
Figuring out the most suitable light weight aluminum alloy for your application will indicate evaluating a wide selection of features. The initial group addresses alloy attributes that impact the production procedure.
The Greatest Guide To Alcast Company
The alloy you select for die casting directly impacts numerous facets of the spreading process, like just how simple the alloy is to deal with and if it is susceptible to casting defects. Hot cracking, additionally understood as solidification splitting, is a regular die spreading issue for aluminum alloys that can cause interior or surface-level tears or fractures.
Particular light weight aluminum alloys are much more at risk to hot cracking than others, and your selection ought to consider this. It can harm both the actors and the die, so you need to look for alloys with high anti-soldering properties.
Deterioration resistance, which is currently a notable attribute of light weight aluminum, can vary considerably from alloy to alloy and is a crucial characteristic to consider depending upon the ecological problems your product will be exposed to (Casting Foundry). Wear resistance is another building commonly looked for in light weight aluminum items and can set apart some alloys